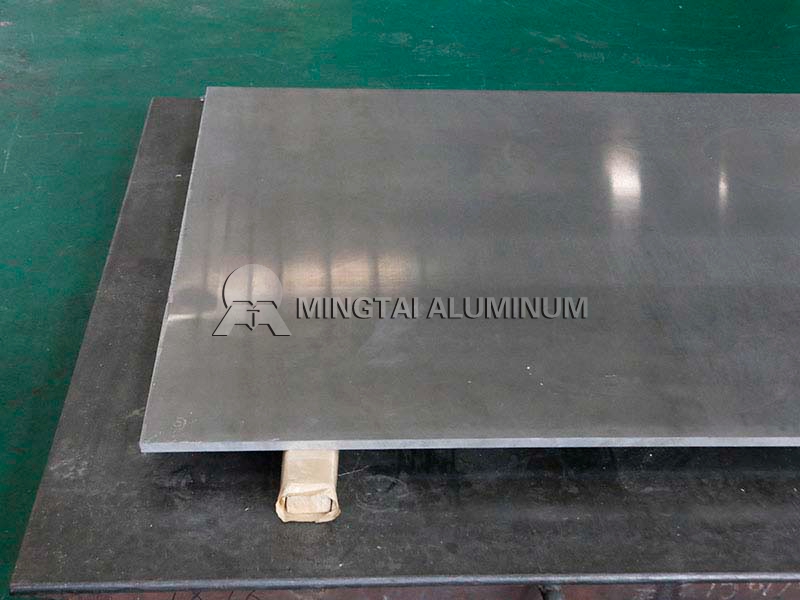
Aluminum characteristics
Sample: A4 Sized
Payment Terms: L/C,D/P,T/T
Delivery time: Within 15-30 Days
Email Us:sale06@mingtai-al.com
(1) Aluminium has a strong affinity with oxygen
It is very simple in the air to form a fine and strong alumina film with a thickness of about 0.1μm and a melting point of up to 2050°C, far exceeding the melting point of aluminum and aluminum alloys, and the density is very high, about 1.4 times that of aluminum. In the welding process, the aluminum oxide film prevents the excellent connection between the metals and is easy to form a slag. The oxide film also adsorbs moisture, which promotes the weld to form pores during welding. These shortcomings will reduce the function of the welded joint. In order to ensure the quality of the welding, it is necessary to strictly arrange the oxides on the outer surface of the weldment before welding and avoid re-oxidation during the welding process. It is useful for protecting the molten metal and the metal at high temperature. This is a welding of aluminum and aluminum alloy. Important features. The detailed maintenance method is to use mechanical grinding or chemical method D40 to remove some oxides from the groove and surrounding parts before welding; use qualified maintenance gas for maintenance during welding (eg 99.99% Ar).
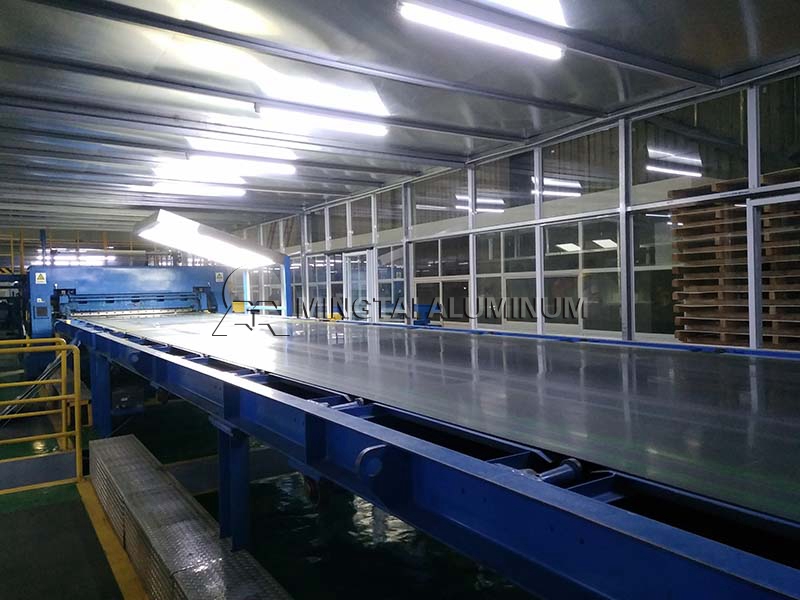
(2) The thermal conductivity and specific heat of aluminum
Although the melting point of aluminum and aluminum alloy is much lower than that of steel, the thermal conductivity and specific heat capacity of aluminum and aluminum alloy are very large, more than double that of steel. During the welding process, many heat energy is agilely transmitted to the interior of the group metal. In order to obtain high-quality welded joints, it is necessary to use heat sources with high energy collection and high power. For thick plates of 8mm and above, preheating and other technical methods are required to complete the welding process.
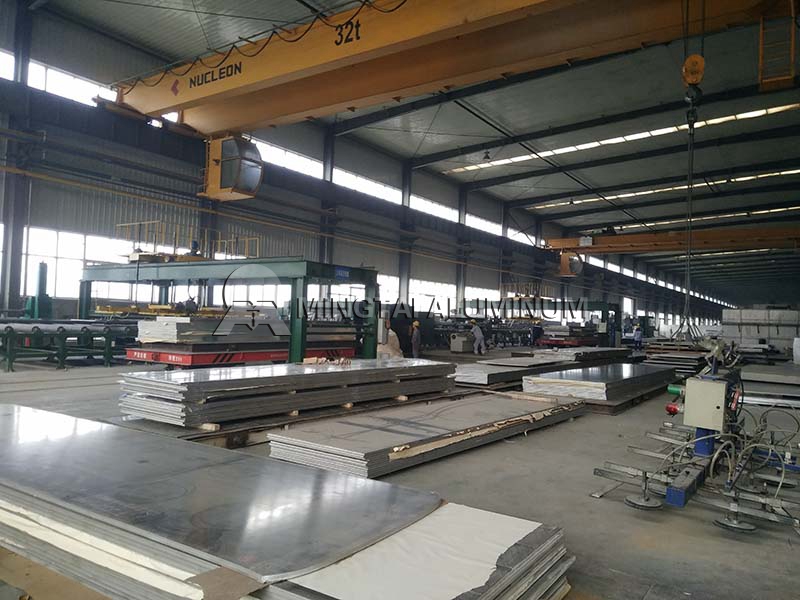
(3) Large coefficient of linear expansion
The linear expansion coefficient of aluminum and aluminum alloy is about twice that of steel, and the volume reduction rate during condensation is 6.5% to 6.6%, which is prone to weld deformation. A useful way to avoid distortion is to choose the right welding tool in addition to the selection of reasonable technical parameters and welding sequence, especially when welding thin plates. In addition, some aluminum and aluminum alloys have a tendency to form crystal cracks in the weld metal and a tendency to form liquefaction cracks in the heat-affected zone, often in the brittle temperature range due to excessive internal stress. Thermal cracking occurs inside, which is one of the most common severe defects in the welding of aluminum alloys, especially high-strength aluminum alloys. The way to avoid such cracks in the internship welding site is mainly to improve the joint drawing, select reasonable welding technical parameters and welding order, and select welding filling materials with customary base materials.
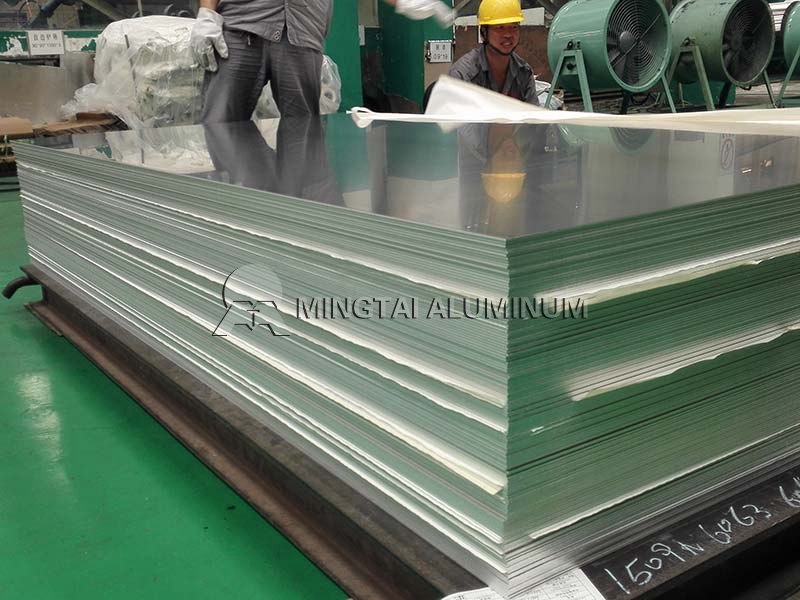
(4) Simple formation of stomata
The pores in the welded joint are shortcomings that occur when aluminum and aluminum alloys are welded, especially for the welding of pure aluminum and rust-proof aluminum. Hydrogen is the main cause of porosity in the welding of aluminum and aluminum alloys, which is now proven by the internship. The origin of hydrogen is mainly the moisture in the atmosphere of the arc column, the welding data and the moisture adsorbed by the base material. The moisture adsorbed by the welding wire and the outer oxide film of the base material often occupy an outstanding position for the occurrence of weld pores. The liquid pool of aluminum and aluminum alloy absorbs pores very simply. Many gases dissolved in high temperature have a sharp decrease in solubility when condensed by liquid. In the process of cooling and condensation after welding, the gas is too late to be separated and collected in the weld. Form the pores. In order to avoid the occurrence of pores, in order to obtain outstanding welded joints, the origin of hydrogen should be strictly controlled. It is necessary to strictly limit the water content of the welding materials (including welding wire, welding rod, flux, maintenance gas) before welding. It is necessary to carry out rigorous disposal, and the finished base metal and welding wire should be welded within 2 to 3 hours, and the maximum is not exceeded 24 hours. For TIG welding, a large welding current is used in conjunction with a higher welding speed. For MIG welding, a large welding speed with a slow welding current is selected to improve the existence of the molten pool.
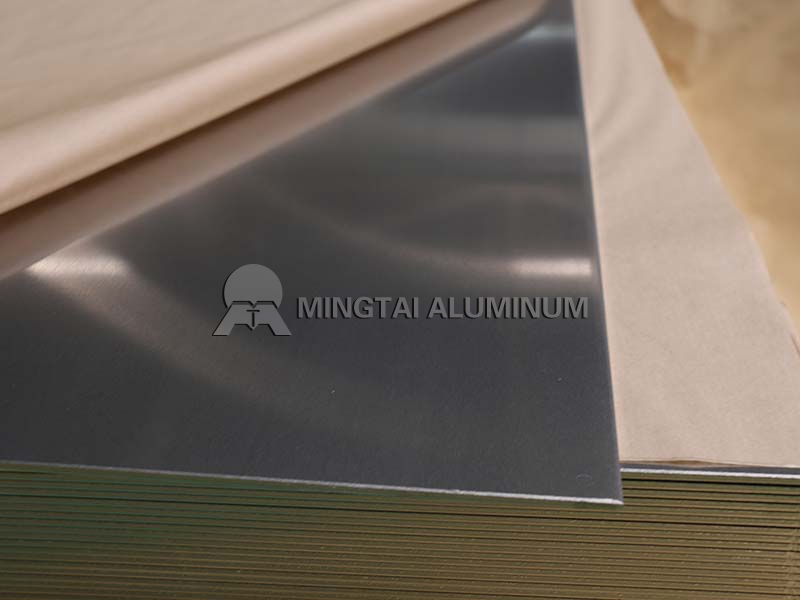
(5)Strength and plasticity of aluminum at high temperature Low aluminum has a strength of only 10 MPa at 370 ° C. When welding, the weld metal may not be supported due to the inability to support the liquid metal, and even form a collapse or burn through. In order to deal with this problem, it is often necessary to use a backing plate when welding aluminum and aluminum alloys.
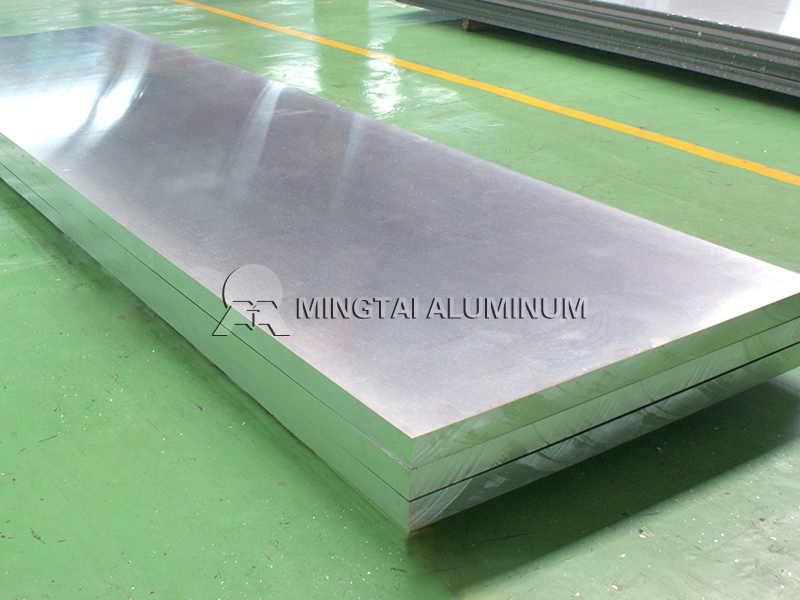
(6) No color change, which brings difficulties to the welding operation.
When aluminum and aluminum alloys are converted from solid to liquid during welding, there is no significant color change, which brings a lot of difficulty to the operator during the welding process. Therefore, the demand welder grasps the heating temperature at the time of welding, and uses the flat welding as much as possible to introduce (receive) the arc on the lead (receive) arc plate.