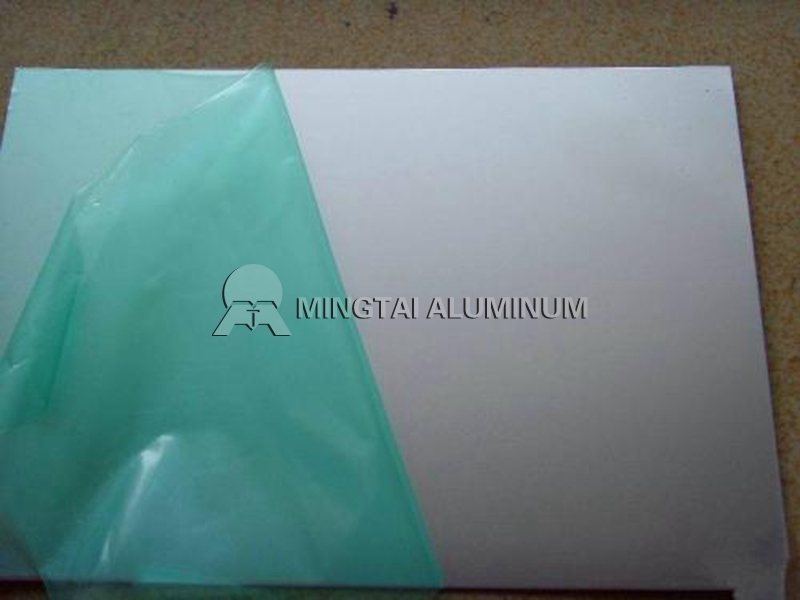
Anodized aluminum plate pretreatment
Sample: A4 Sized
Payment Terms: L/C,D/P,T/T
Delivery time: Within 15-30 Days
Email Us:sale06@mingtai-al.com
The anodized aluminum plate pretreatment process is an important part to determine the appearance quality of the product. The various quality requirements such as the removal of the mechanical grain of the profile, sanding, matt, and glazing are determined by the pretreatment process.
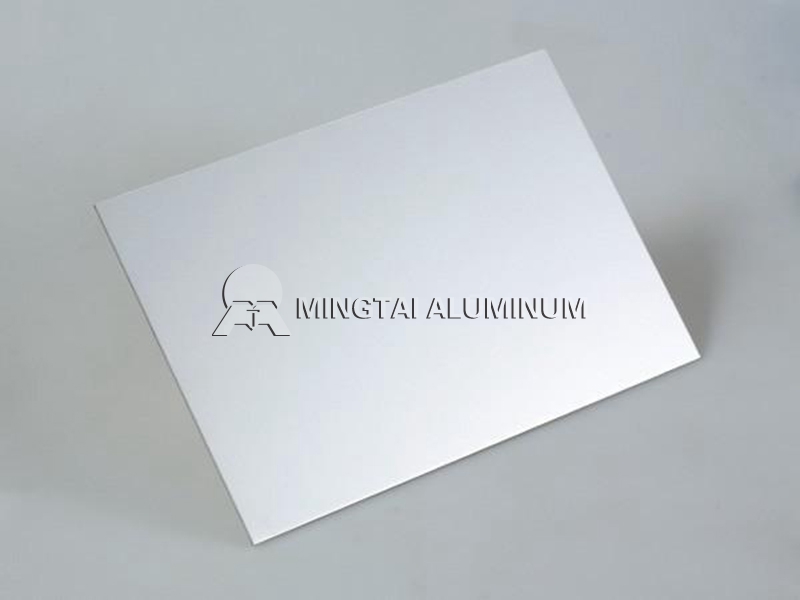
Anodized aluminum plate pretreatment four major processes:
1.Polishing process: After the aluminum plate is degreased, it is placed in the polishing tank. After polishing for 2-5 minutes, it can form a mirror surface, which can be directly oxidized after washing. The core process of the process is polishing, de-graining, mirroring, all done in the polishing bath. Polishing has the advantages of low aluminum consumption and bright profile, but the NOx escape from the polishing bath causes serious environmental pollution and physical injury to the operator. At the same time, the cost of expensive chemical raw materials also restricts the promotion of the process.
2.Alkali etching process: anodizing can be performed by removing the mechanical grain and the natural oxide film and sanding by alkali etching in the alkali etching tank, and then removing the surface black ash through the light exiting groove. However, this process is high aluminum consumption, which wastes resources and brings serious environmental problems and increases wastewater treatment costs. The process has been used for more than 100 years, and most of the world’s aluminum plate manufacturers have been in use until now, and it has been gradually replaced by acid etching until the past two years.
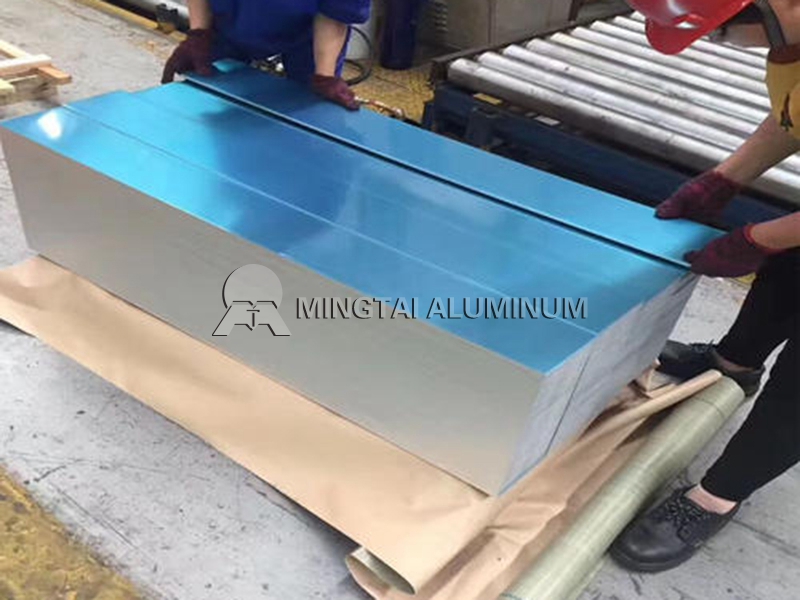
3.Acid etching process: After the aluminum plate is degreased, it is firstly etched, then alkali etched, and the light is discharged to complete the pretreatment. The biggest advantage of acid etching is that it has strong mechanical graining ability, quick sanding and low aluminum consumption. However, the environmental protection problem of acid etching is more prominent. Also, after acid etching, it will cause the appearance of aluminum plate to be dark and dark. These problems have been There is no effective solution yet.
4.Leveling and Brightening Process The so-called leveling and brightening process is a new surface pretreatment process introduced after polishing, alkali etching and acid etching. It is a profound transformation and transformation of the alkali etching and acid etching process. Acid-etched aluminum has the advantages of low consumption, strong mechanical graining ability and quick sanding, and has a polished and bright. The leveling and brightening process is much simpler than acid etching and alkali etching, and even simpler than the polishing process, eliminating the polishing NOx. Pollution, acid etching fluoride pollution, alkali corrosion alkali slag pollution and other drawbacks.
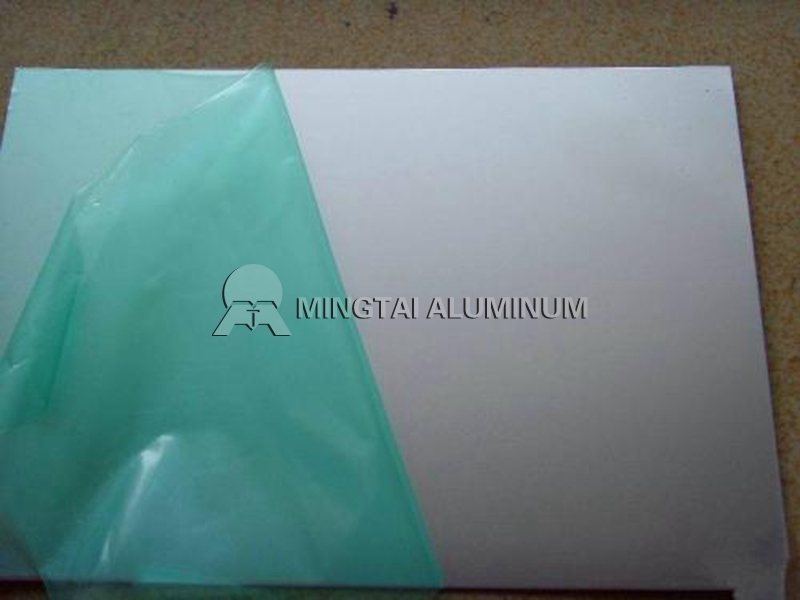
Advantages of anodized aluminum plate:
A thin layer of aluminum oxide is formed on the surface of the anodized aluminum plate, and the thickness thereof is 5 to 20 μm, and the hard anodized film is 60 to 200 μm. The anodized aluminum plate improves the hardness and wear resistance, up to 250-500 kg/mm 2 , good heat resistance, the hardness of the hard anodized film is as high as 2320K, excellent insulation, and high breakdown voltage 2000V, enhanced corrosion resistance, does not corrode in thousands of hours in the salt fog of ω=0.03NaCl.