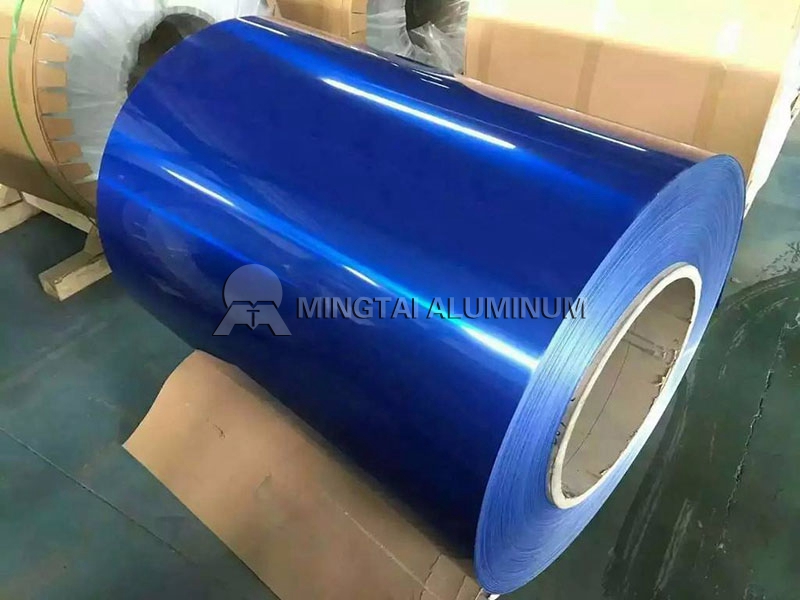
Coated Aluminum Coil | Coated Aluminum Plate
Sample: A4 Sized
Payment Terms: L/C,D/P,T/T
Delivery time: Within 15-30 Days
Email Us:sale06@mingtai-al.com
Introduction to Coated Aluminum Coil:
Coated aluminum coil is also called organic coated aluminum plate. It is made of aluminum coil and aluminum plate as substrate, coated or laminated with various organic paints or plastic films. Because it is a surface-coated coil in a metallurgical plant that can be directly processed into a product, it is also called pre-coated coil.
Advantages of Coated Aluminum Coil:
The coated plate combines the advantages of both organic polymer and steel plate, and has good coloring property, moldability, corrosion resistance, decorative property of organic polymer, high strength and easy processing of aluminum plate, and can be easily punching, bending, deep drawing, welding etc,. This makes the product made of organic Coated aluminum coil excellent in practicality, decoration, processability and durability.
Application of Coated Aluminum Coil:
Coated aluminum coil in the use of a wide range, including use in building (aluminous model board, aluminum honeycomb, wave plate, roof fire stick panel, aluminum ceiling, blinds, doors, garage doors, awning, the water gutter), electronic appliances, computer case, electrical panel), solar reflector, decorative lighting, furniture, air conditioning duct, leftover material and cans, etc.
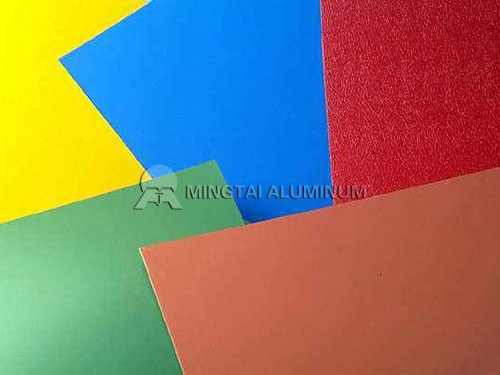
Typical Production Process for Coated Aluminum Coil:
The whole unit consists of the following four parts: the inlet section, the pretreatment section, the painting section and the outlet section. The common two-coating two-bake color coating production line process is: unwinding → sewing → inlet looping → cleaning → pre-treatment → initial (fine) coating → initial (fine) curing → cooling → export looper → shear → volume take.
Inlet section: including unwinding, trimming, seaming and stocking loopers, etc., the function is to loosen the raw material rolls and join them together to supply the metal sheet continuously and uniformly to the unit.
Pretreatment section: The coated substrate is cleaned and surface treated to improve corrosion resistance and adhesion to the upper paint film.
Painting section: It is the core part of the whole unit. It usually adopts two-coating and two-bake process of simultaneous coating on both sides, ie, primer (priming) → baking and curing → cooling → coating (fine coating) → Bake curing → cooling. Depending on the product requirements, you can also apply one coat or only one side. Reverse or smooth roll coating can be used for painting. The furnace temperature is controlled in stages, and the temperature of each section depends on the type of coating used, the thickness of the bottom plate, and the time of passing the oven.
Export section: The product is divided into volumes (or cut into individual sheets according to the required size).