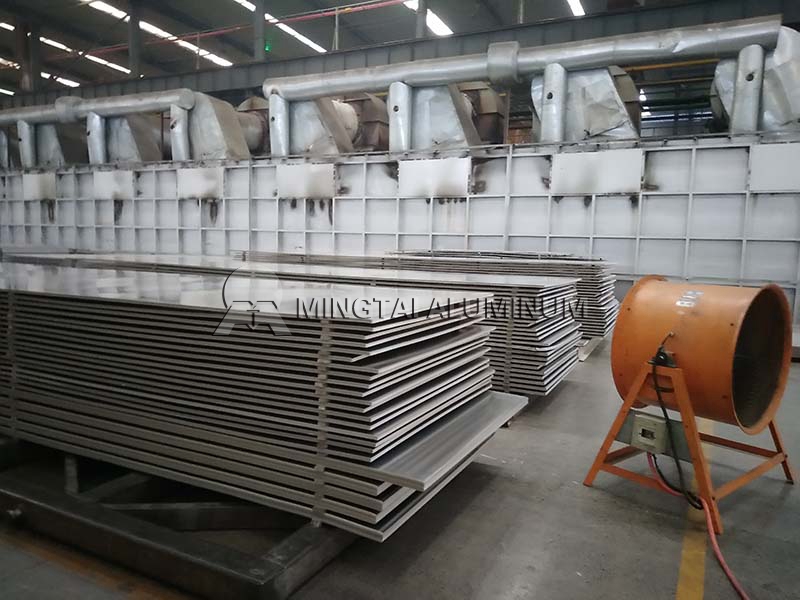
Hot rolled billet processing technology
Sample: A4 Sized
Payment Terms: L/C,D/P,T/T
Delivery time: Within 15-30 Days
Email Us:sale06@mingtai-al.com
Hot rolled billet mainly uses semi-continuous and continuous production methods to produce aluminum ingots. Most of the modern hot-rolling rolls are produced by semi-continuous casting. The ingots can be produced in heavy weight and ingots. High size, surface, chemical composition and internal quality
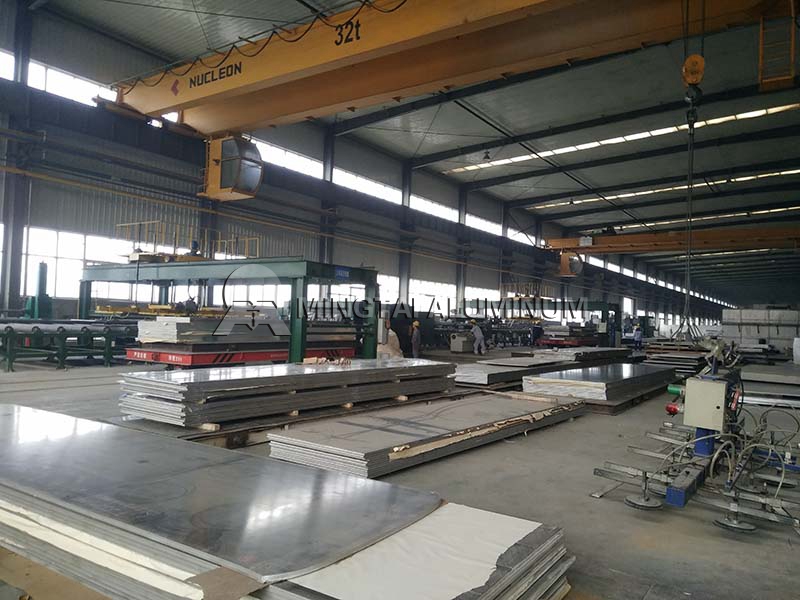
1. the preparation and quality requirements of the ingot.
(1) The selection of ingots should take into account the customer’s quality requirements and their own equipment capabilities and process levels.
(2) Basis for selection of thickness of ingot: thickness and deformation rate of finished product
(3) Basis for selection of ingot width: width of finished product and amount of trimming of alloy
(4) Selection of the length of the ingot: the diameter of the hot rolled coil
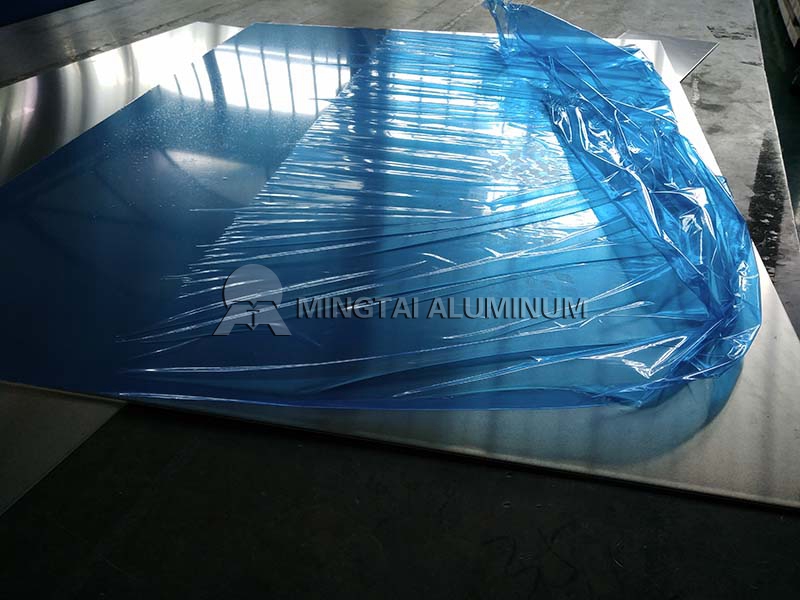
2. the shape of the section of the ingot: (1) circular arc (2) trapezoidal (3) V-shaped (4) rectangular
3. the purpose of the ingot cutting head
4. the treatment of the ingot head and tail before hot rolling
(1) Products with low surface requirements can be processed without any treatment on the ingot casting and bottom.
(2) For products with high surface requirements, all defects in the head and tail casting must be removed.
(3) Determination of the length of the incision of the ingot
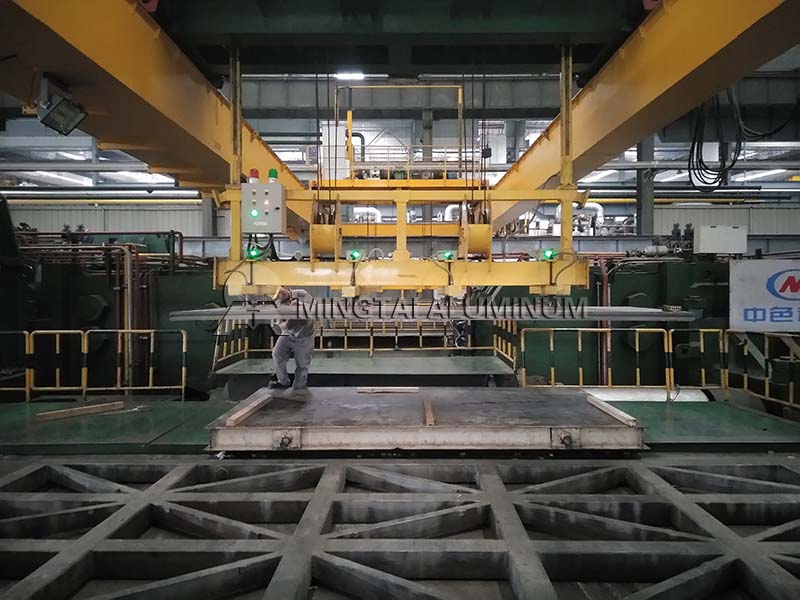
5. Surface treatment of ingots before hot rolling
1, milling surface
The principle of determining the amount of ingot milling: the use of the product, the characteristics of the alloy. Casting technology, the current milling face with side milling is generally 8-15mm. Small face 8-10 mm. Features of milling machine: dry milling and wet milling
2. Surface quality requirements after milling
(1) The ingot face is not easy to bend too much
(2) The control of the milling cutter mark, the depth of the knife mark shall not exceed 0.15MM (3) The surface has no sticky aluminum phenomenon
(4) No bumps or long storage time